MORPHOLOGY STUDIOS 2017-18
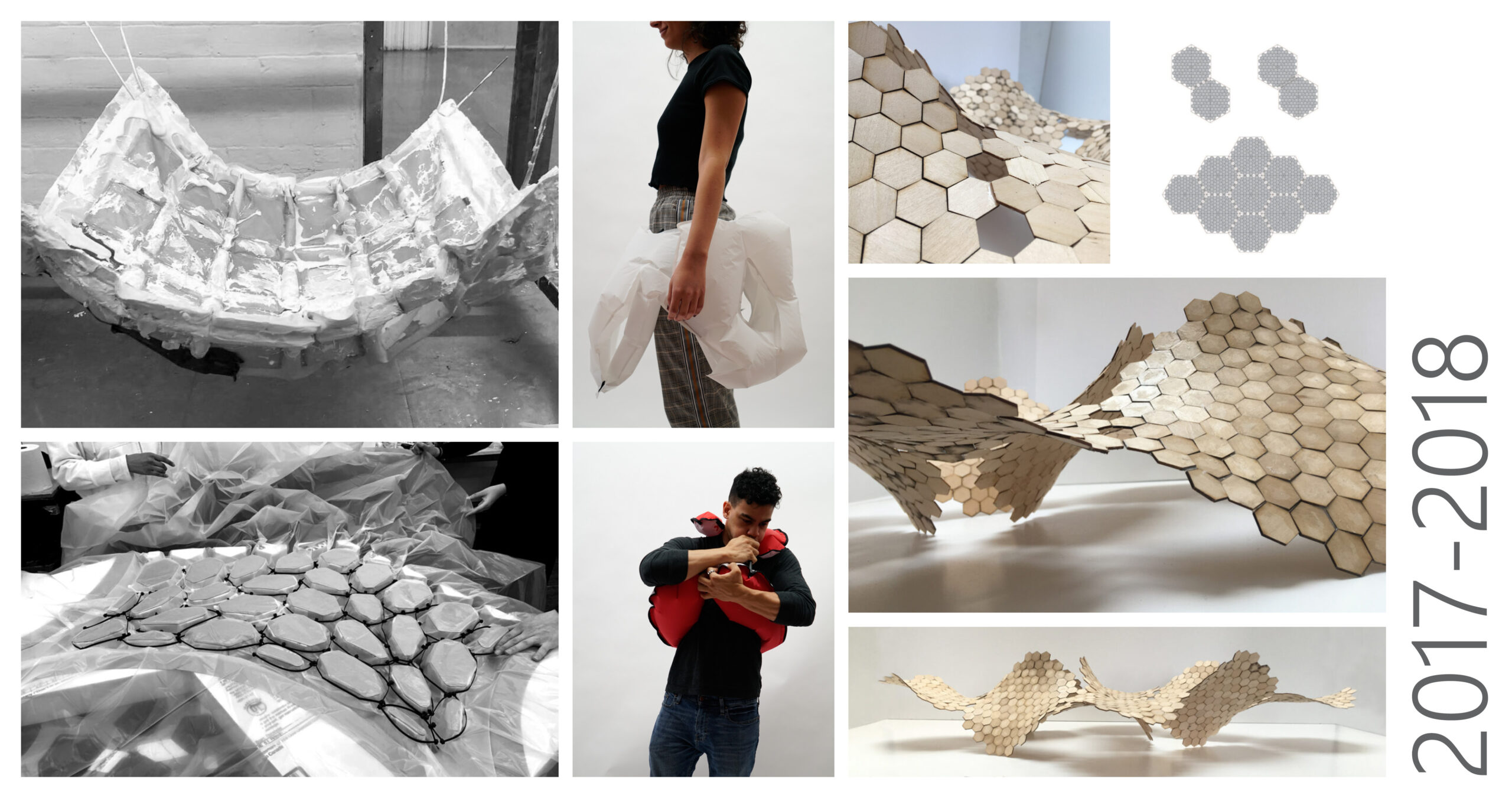
FORM AND FORCE
INFLATABLE FORMWORK
Students in this seminar explored inflatable bladders as flexible formwork for casting cementitious structures. The formwork was suspended from pouring points at certain corners to allow the mesh to deform into catenary shells under gravity. Heat sealing patterns were developed to channel the mix into the bladders and direct structural forces through the grid shell. Students also tested woven aircraft cable and networked zip-ties as strategies for integral reinforcement.
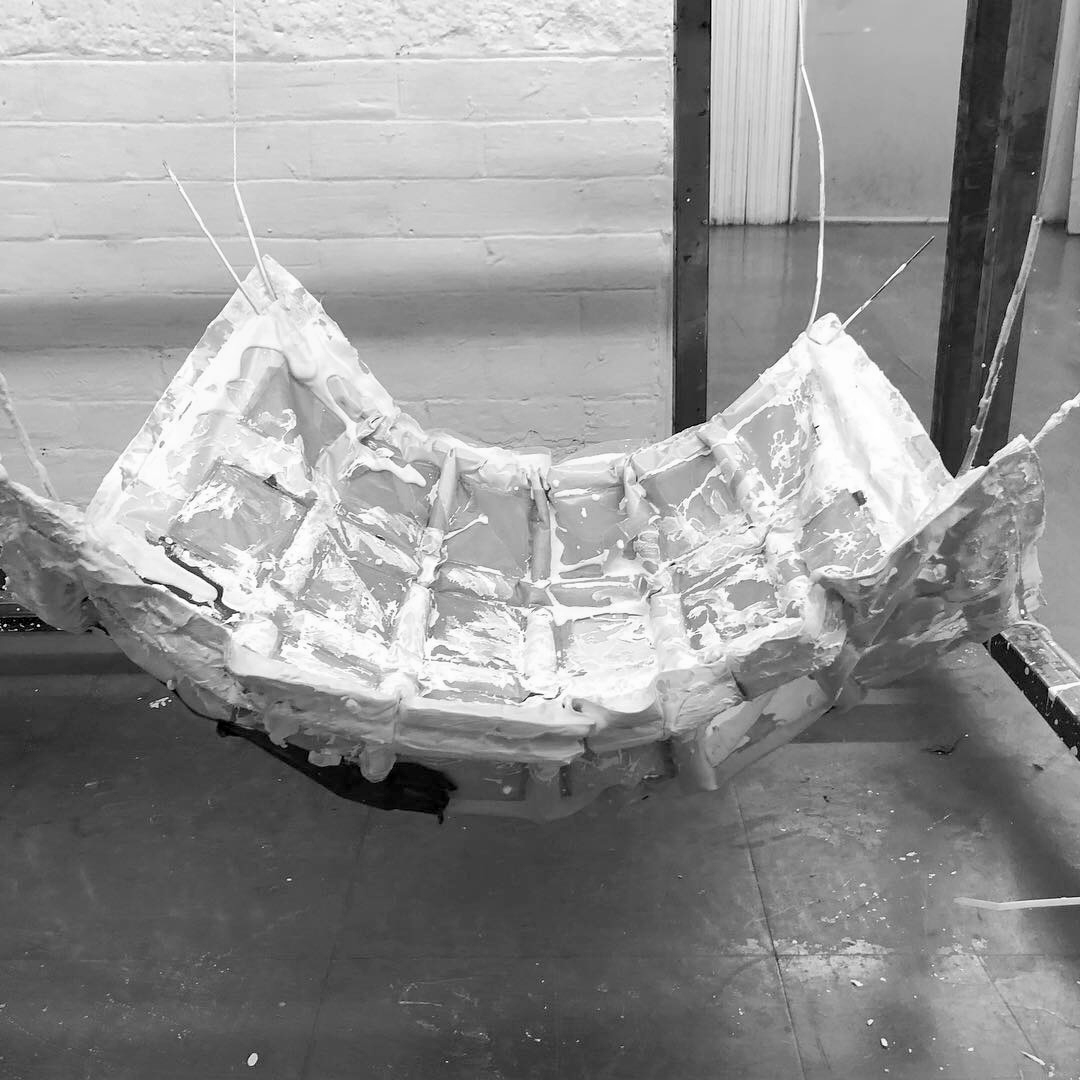
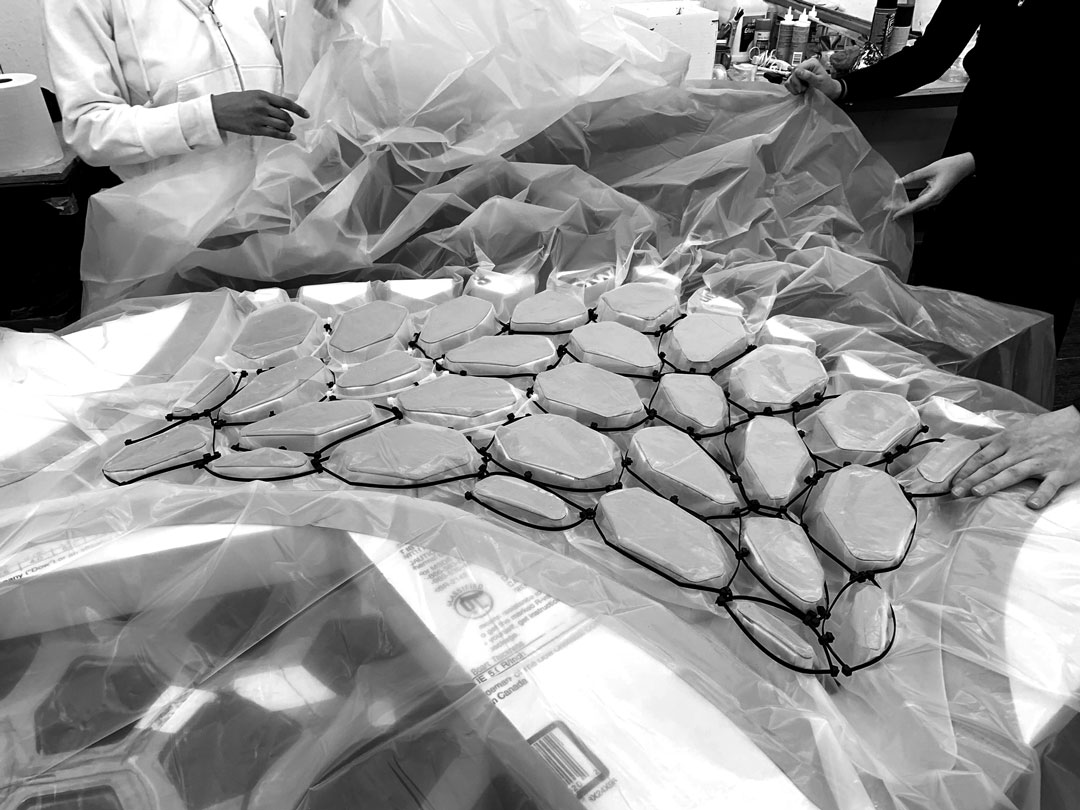
[Credits]:
Faculty: Ajmal Aqtash (with Robinson Strong)
Students: Iyatunde Majekodunmi, Vahhab Aboonour, Andes Plasencia, Aisha Aljassim, Liubou Lucy Zakharova, Aaron Miranda, Matthew Malcolm, Kalam Lin Siu
FORM AND TIME
PNEUMATIC ORIGAMI (5)
In this course, students designed and built self folding (and unfolding) structures using a combination of thick origami and inflatable bladders. Thick rigid panels were assembled to mimic thin paper origami patterns while accounting for material thickness. A custom heat sealed bladder was then attached to the thick origami panels. Inflating the bladder unfolds the structure and springs return the structure to its folded state when the bladder’s air pressure is returned to the atmosphere.
PNEUMATIC WEARABLES (1-4)
In this course, students focused on building flat heat-sealed patterns that fold when inflated. We used various heat sealing techniques including our custom CNC heat sealing machine to create intricate self-folding patterns in LDPE and TPU backed nylon. Digital pneumatic controls were also introduced to create interactive installations that inflate in response to touch.
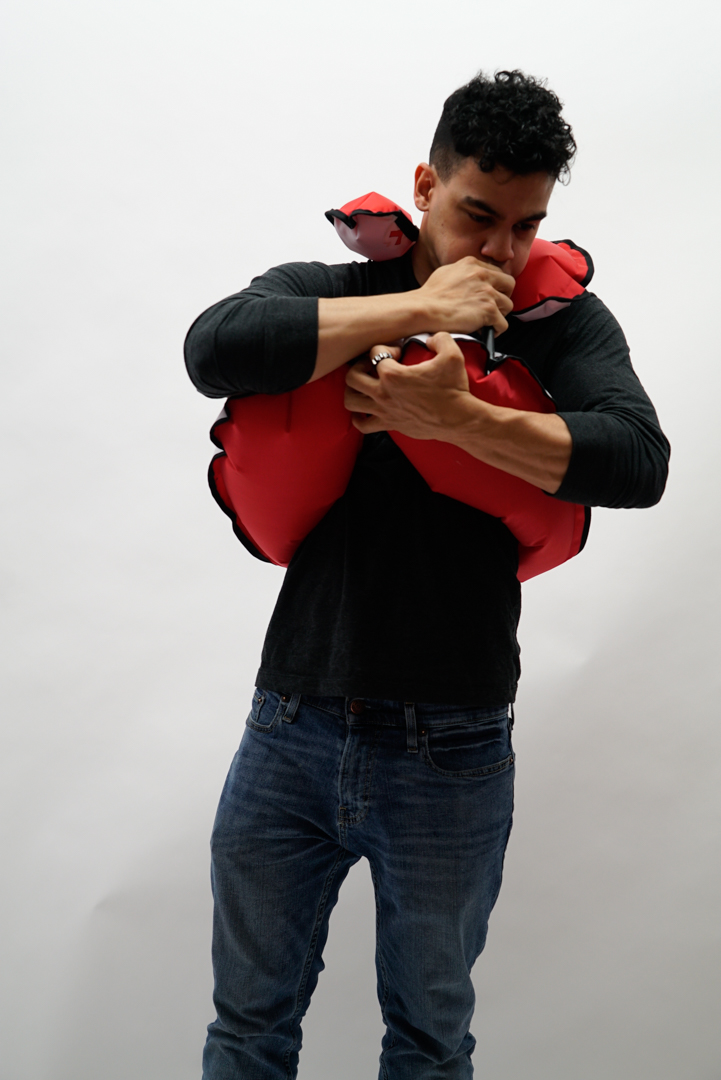

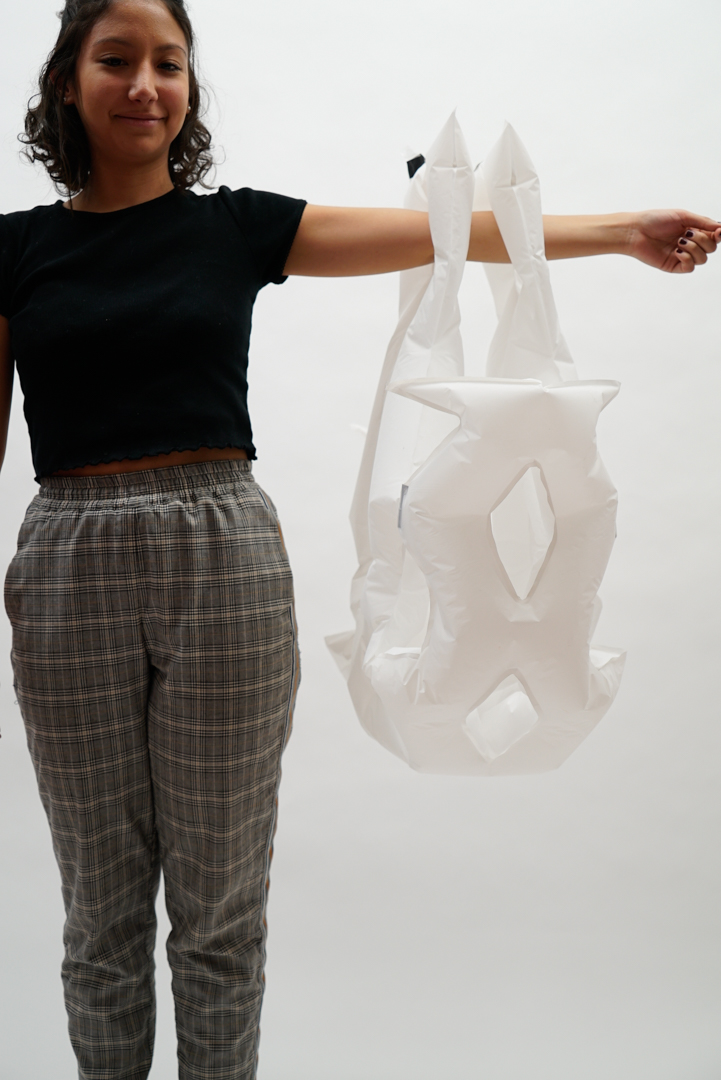
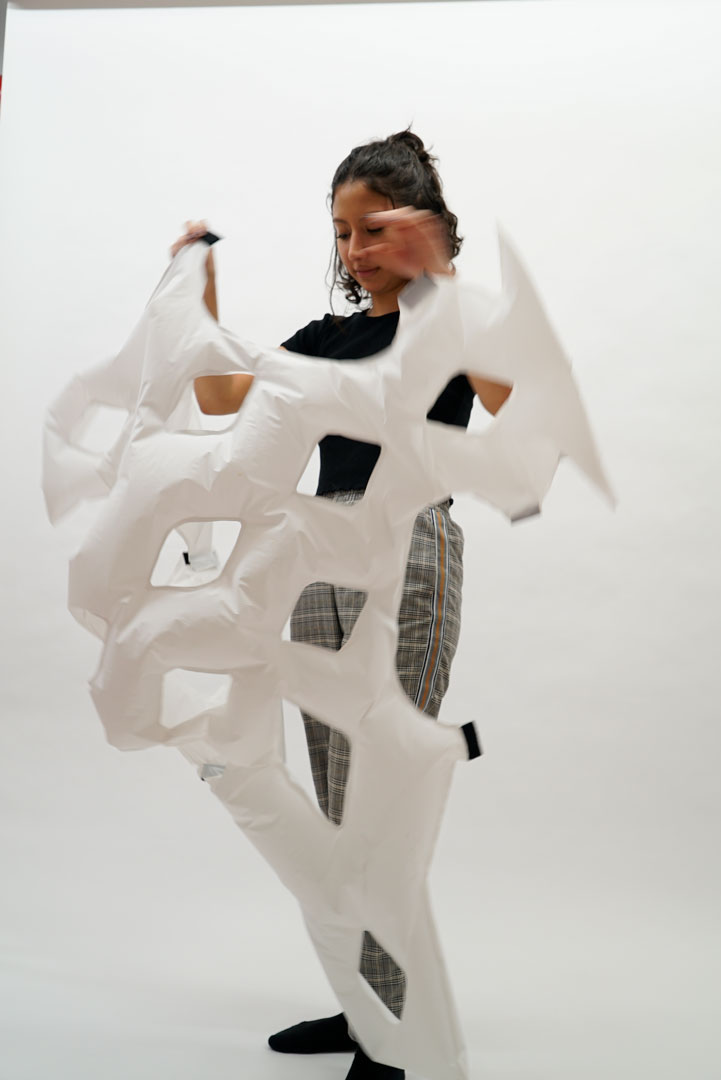

Credits]:
Faculty: Che-Wei Wang
Students: Tomas Castelli, Brandon Spinosa (5), Andrew Saldivar (1), Adriana Hinojosa (2-4)
FORM AND SPACE
CURVED SHELLS FROM IDENTICAL MODULES
The standard brick, a 3D rectangular block, permits infinitely variable rectilinear morphologies but also enables complex curved surface morphologies. In 2014-15, we demonstrated the latter with a portion of a curved space-filling minimal surface by introducing interstitial pieces which were dissections of the brick. Here, we returned to that idea and explored the equivalent of non-rectangular “bricks”, all identical to start with (as in plane tessellations), to see if we could build saddle-type structural surfaces which have a negative curvature. We know this cannot be done since gaps will be produced by departing from the flat plane. We challenged ourselves to find an equivalent of the role “mortar” plays in a brick arch, namely, it fills the (slender trapezoid-shaped) gaps between rectangular bricks to enable a curved arch which otherwise won’t be possible. Could we not do the same to any plane tessellation, i.e. fill the gaps between the planar tiling units to build a continuously curved surface with compound curvatures? The shapes of the mortar-shaped gaps, not identical any more as in a circular arch, will be filled with a filler material (as in hardening compounds mimicking mortar, e.g. images 4,11-14) or by adding filler pieces (10) as we did earlier, or alternatively, using any shape accommodating joining device.
The results are surprising. We restricted ourselves to simple regular polygons – squares, triangles and hexagons – with the understanding that once we achieved results with these units, we could introduce additional regular or non-regular polygons. Examples illustrated show various hex saddles, all self-stiffened by curvature, as structural surfaces. Some (4,11-14) have no visible gaps, others have openings (6,7,9), some others are shingled with overlapping tiles (2,3). One of the students (Sean Russo) developed a mapping technique to visually “project” a plane tessellation on a compound curved surface. This enabled a visual guide for constructing some of the saddle surfaces.
We show individual 6-sided saddle units with different tile shapes (1-10). The studies culminated in a group project to produce configurations by joining 9 identical structural saddles, each a 6-sided saddle composed of tiled hexagons and assembling them in 3D space (11-14). By adding a secondary unit, a 4-sided saddle, the resulting structure produces an infinitely extensible minimal surface. We believe this is a new minimal surface composed of two saddle units, 6-sided and 4- sided, discovered by our student Sean Russo. The tiling rule for the tessellated modules for this surface was developed by Naini Bansal with Seokyoung Jung (15, 16).
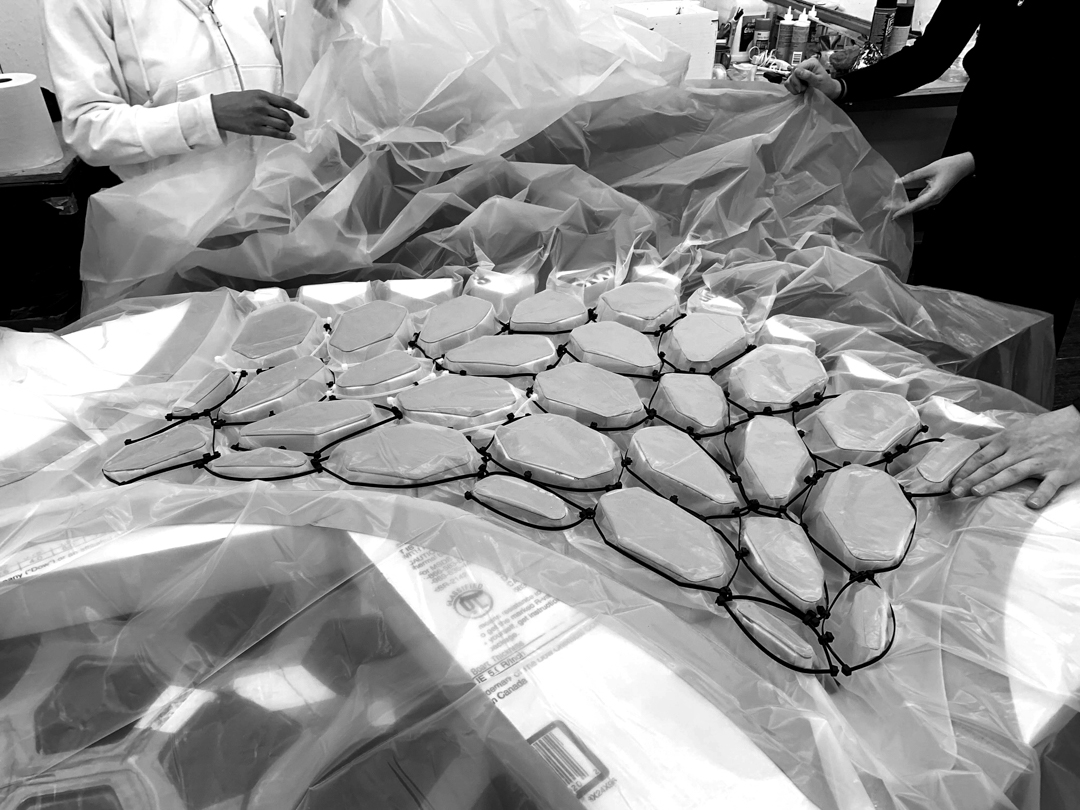
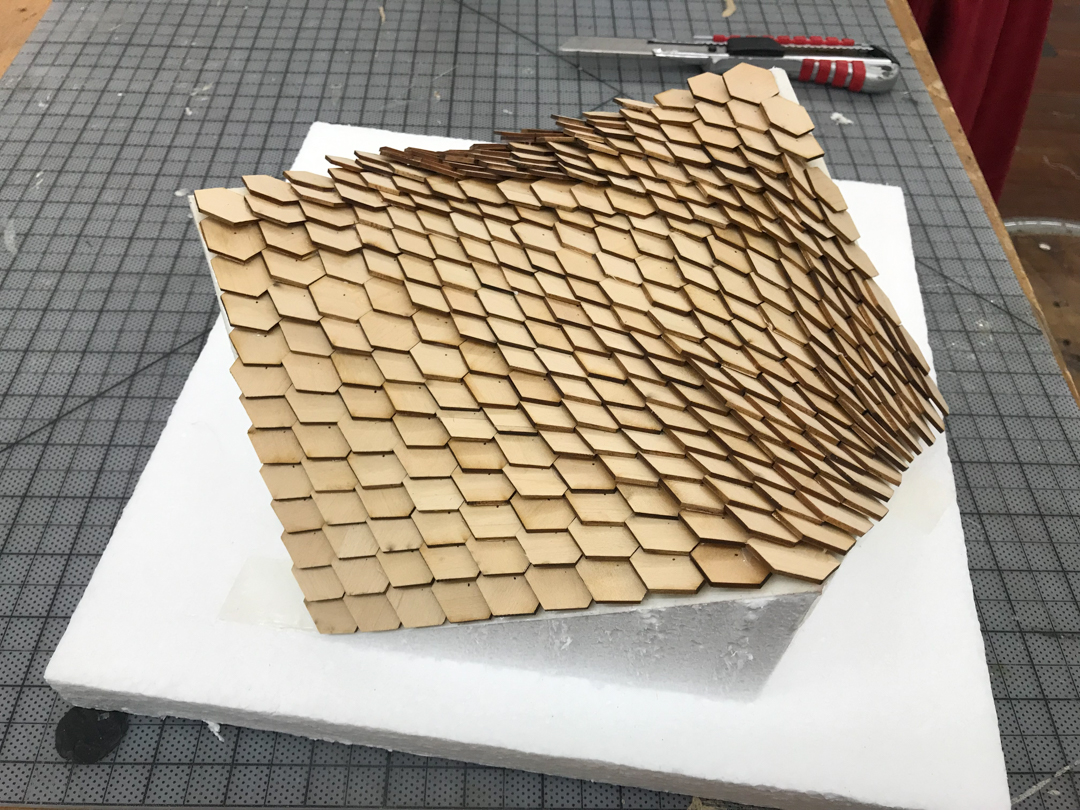
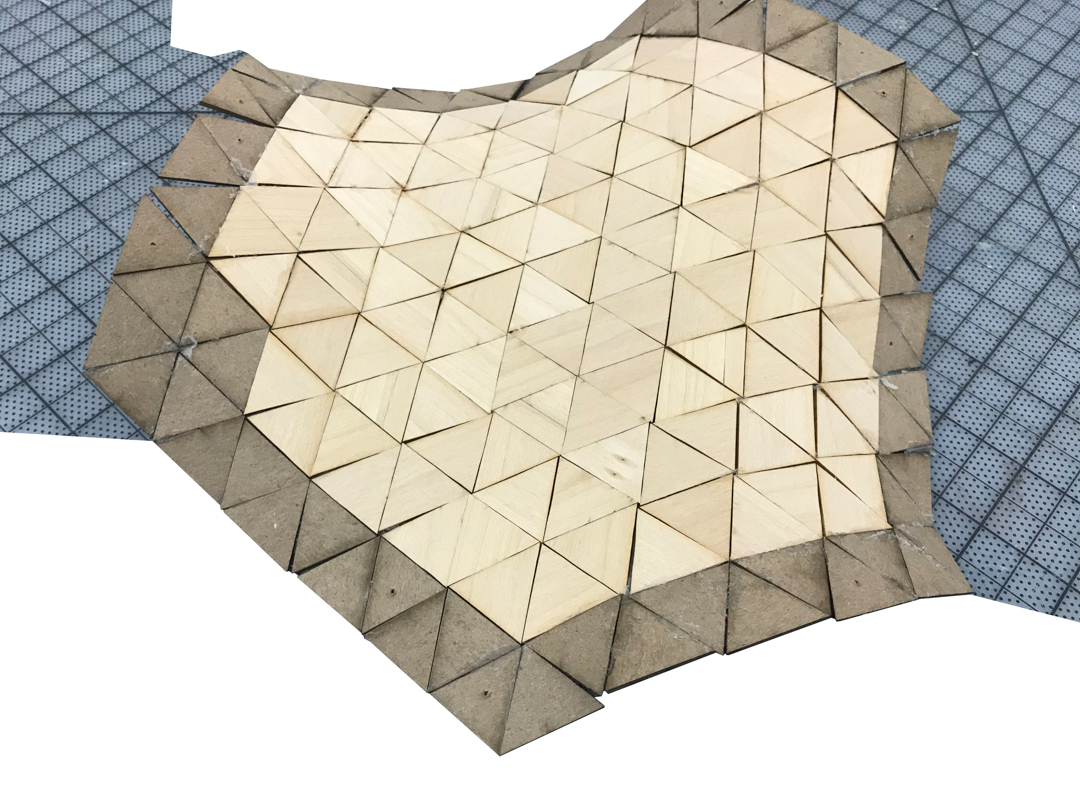
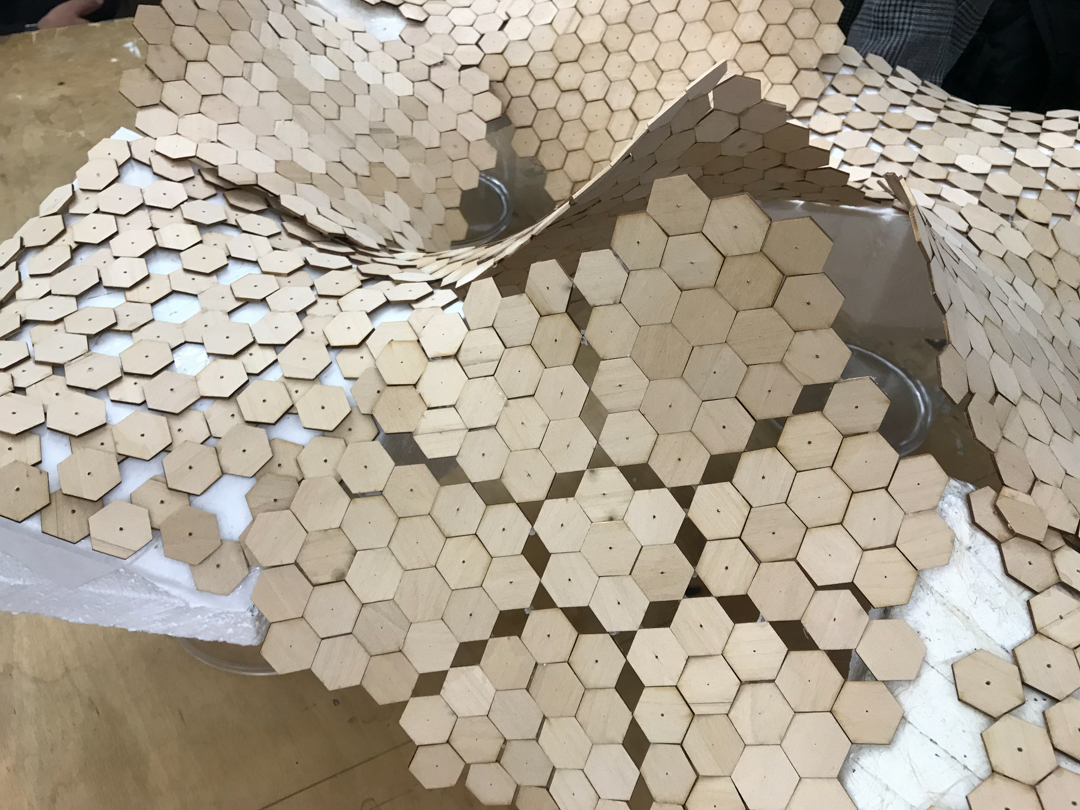
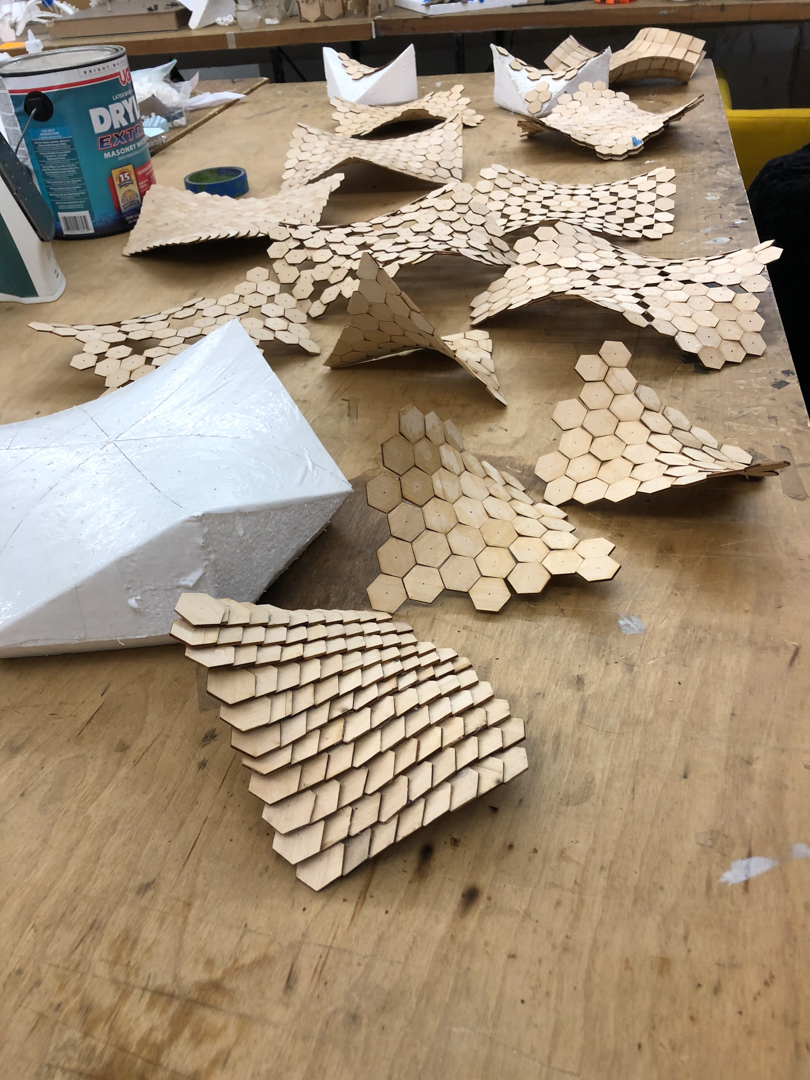
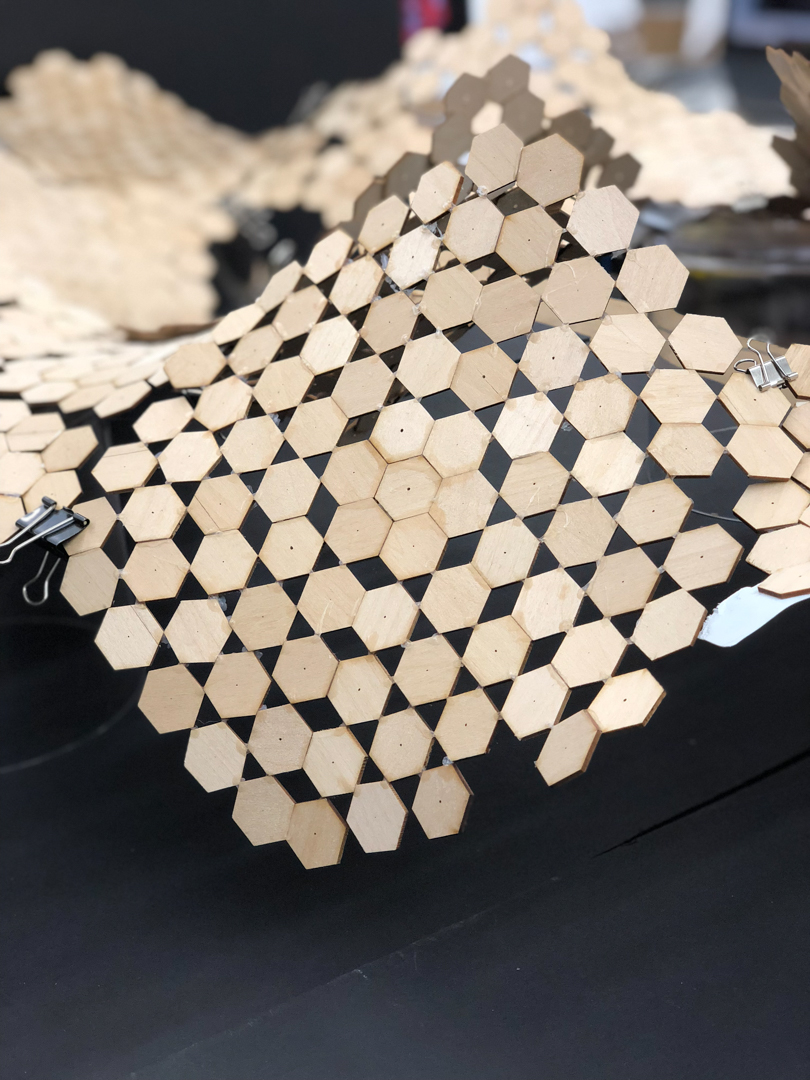

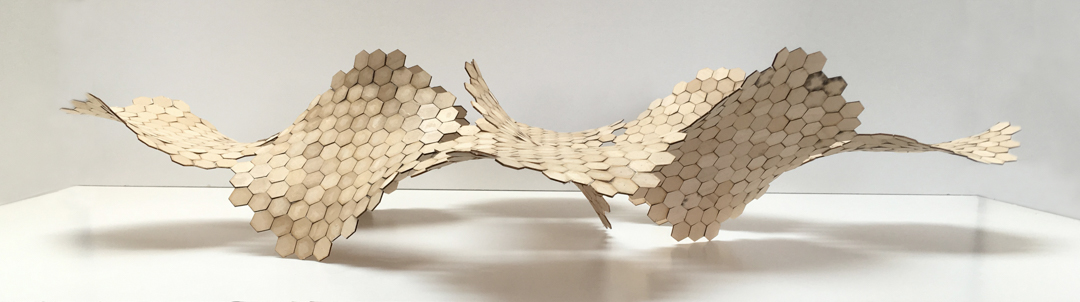
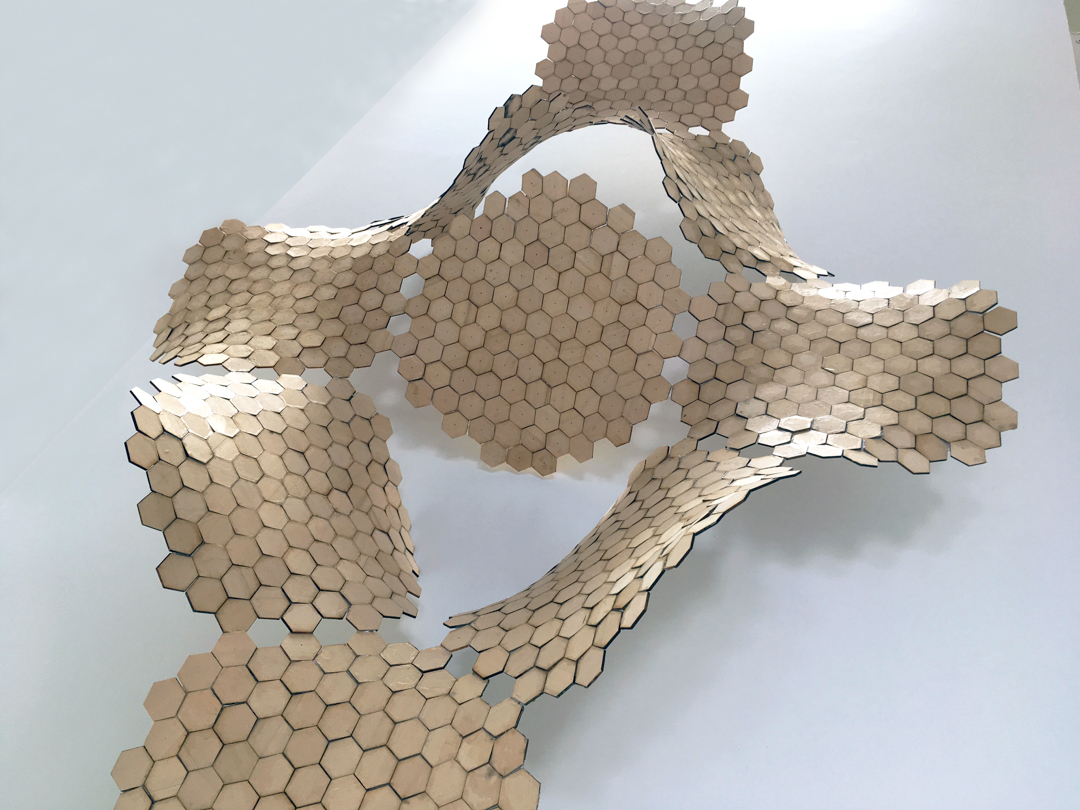
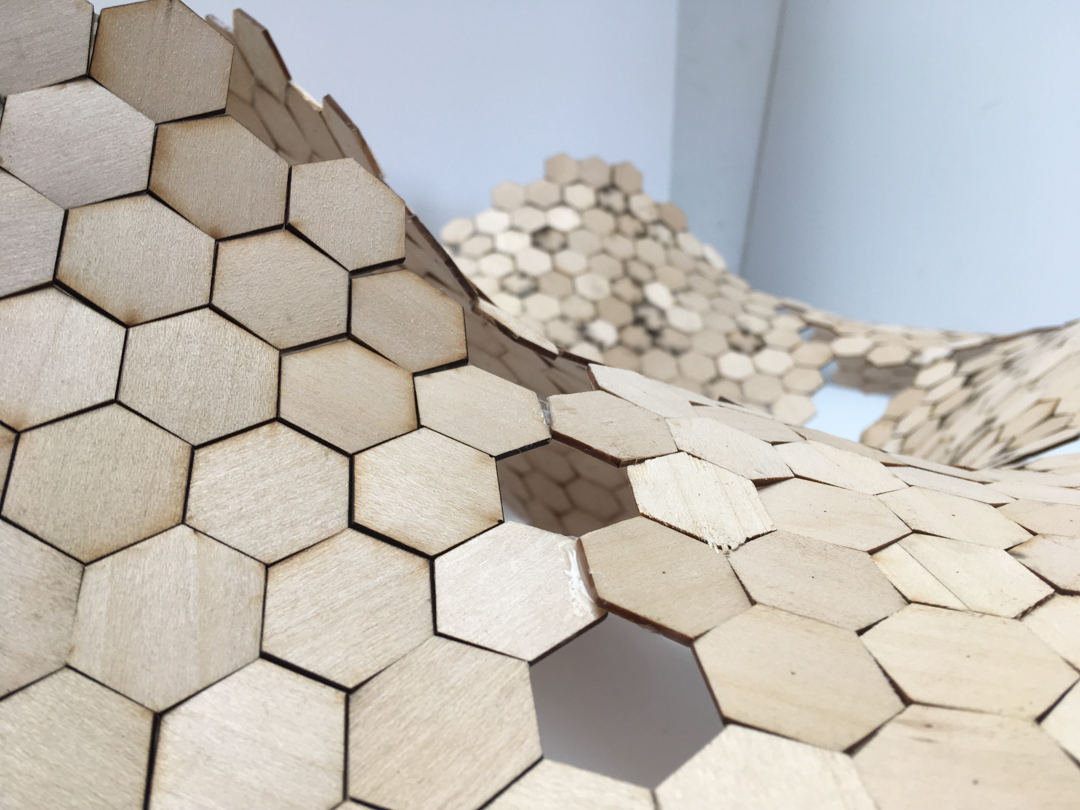
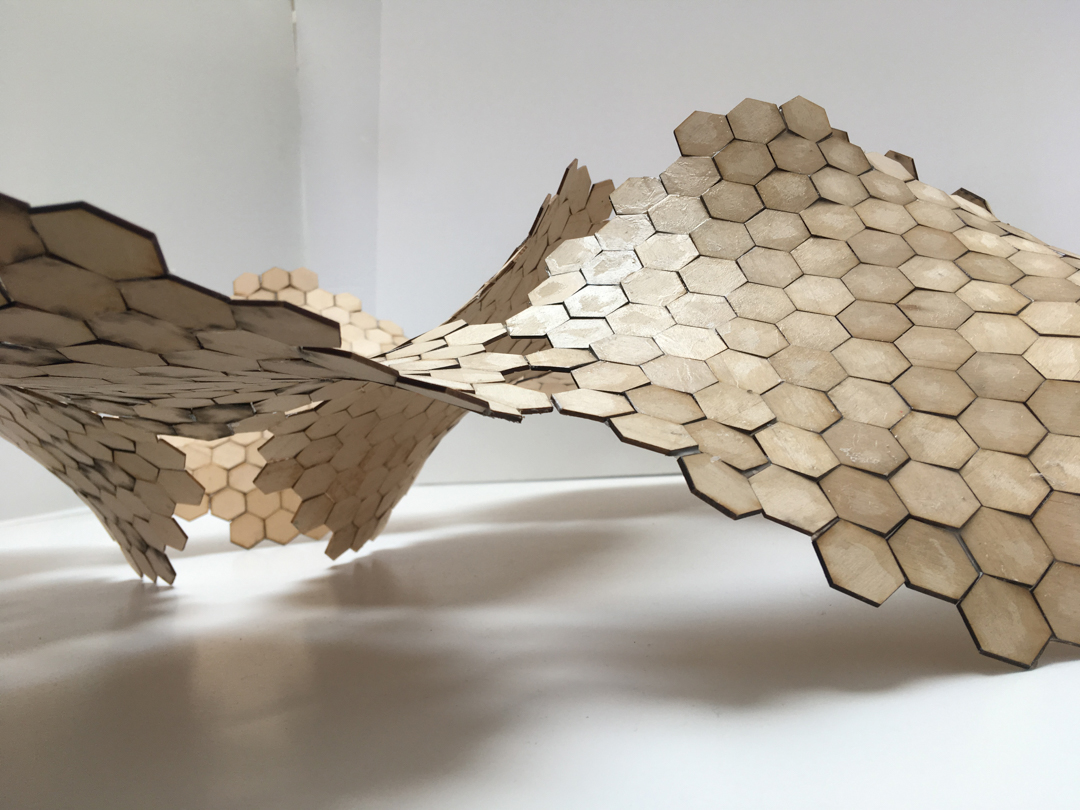
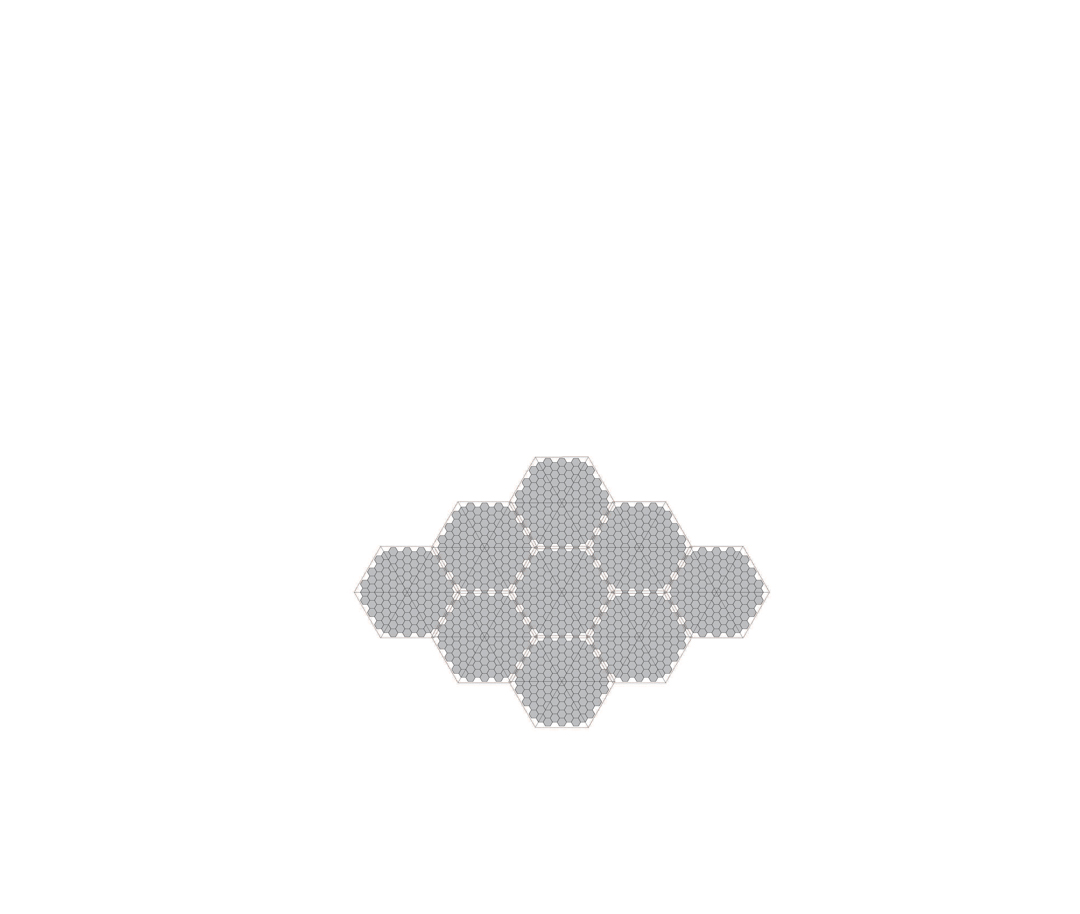
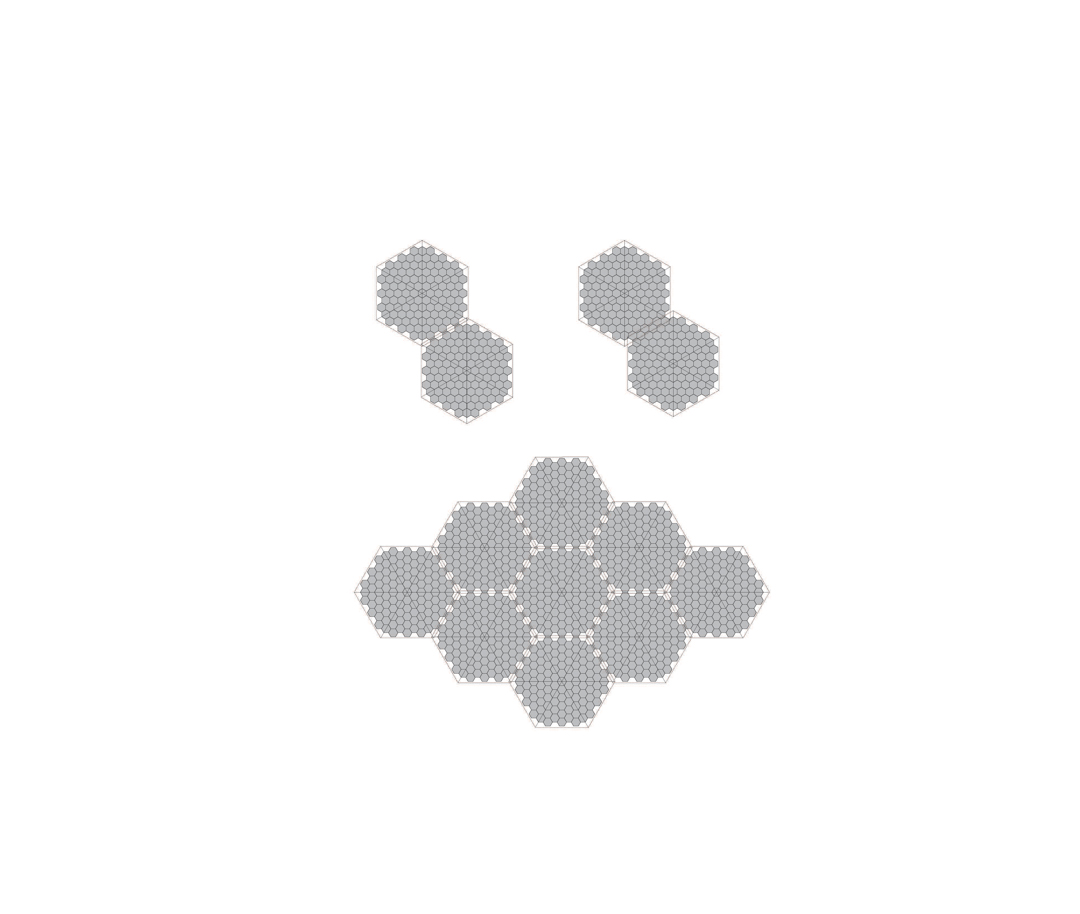
[Credits]:
Faculty: Haresh Lalvani & John Gulliford
Students: Alex Elguera, Seokyoung Jung, Sean Russo, Abhishek Thakkar, Naini Bansal, Gordon Cheng, Ivanna Iriarte