MORPHOLOGY STUDIOS 2015-2016
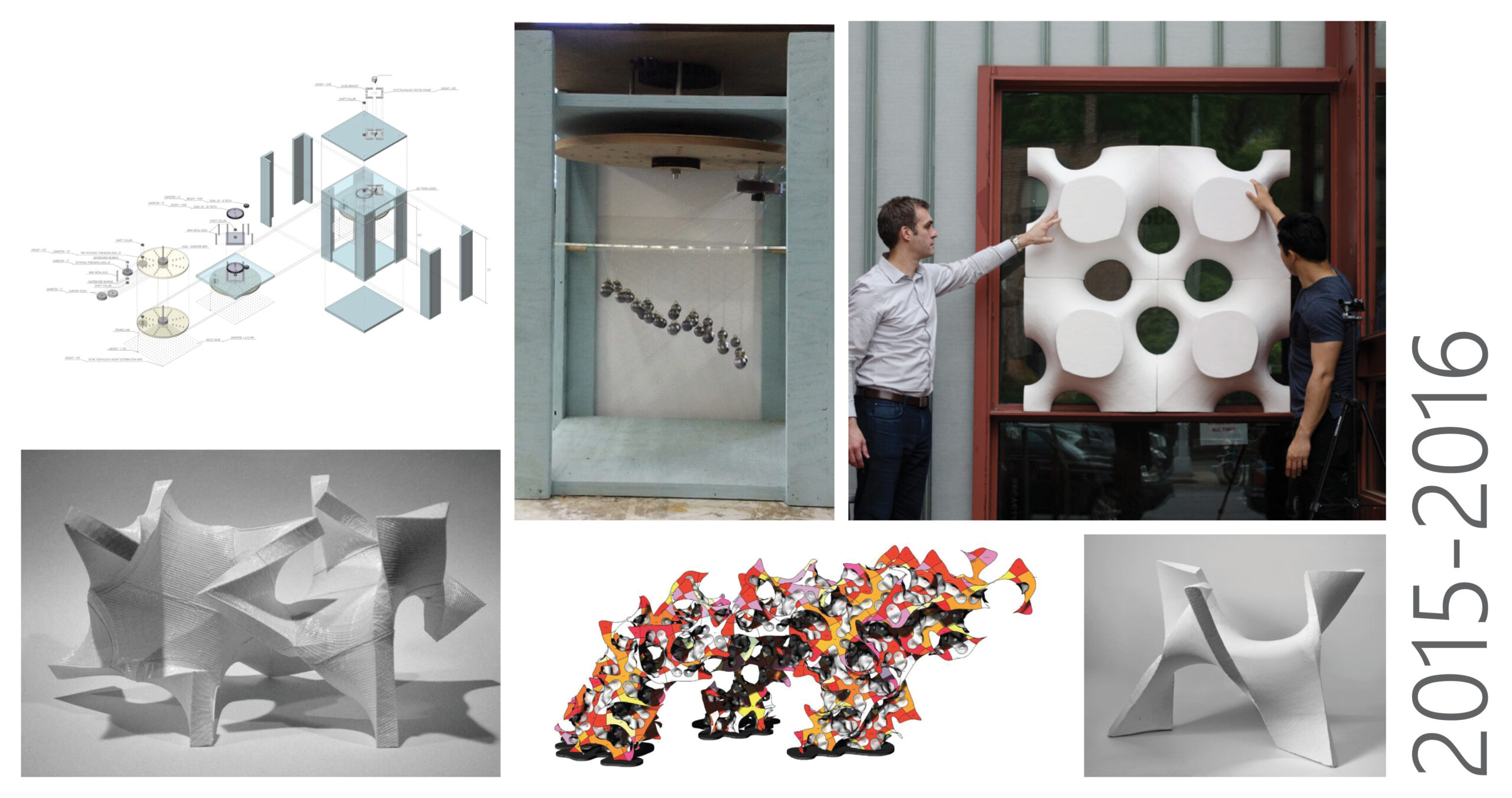
Faculty: Ajmal Aqtash, John Gulliford, Che-Wei Wang, Haresh Lalvani
We continue our explorations into new approaches to spacemaking and space transformations, robotic fabrication and CNC machining, and thermo-forming towards building experimental structures for architecture.
New combinations of mechanisms like cams, levers, linkages (12.13), pulleys (9,10,11) and gears are being studied to prototype and model folded surfaces (14.15) or to build large aggregations of the mechanisms themselves to create kinetic surfaces. Matthew Gardiner’s Oribotics and Ruben Margolin’s kinetic sculptures served as an inspiration. These actuated surfaces have the potential to become walls, floor, and ceilings that actively respond to the way we occupy space.
Our on-going experiment in robotic fabrication of curved surfaces is continuing with the intention of scaling up to building components. We show three examples. A 5-axis robot has been retrofitted with a small router to enable and extend our ability to physically explore minimal surface geometries. These continuously curved forms can be broken into fabricable parts which when assembled visually dissolve the construction logic to build a seamless surface as shown with Fischer-Koch S surface (4-6) or two of Schoen’s S surfaces (7,8). These physical experiments demonstrate that larger aggregates can be constructed and 3d printed to study them. Our objective is to explore how these milled forms can become molds for using new materials (currently, carbon fiber) and develop new structural systems.
In another ongoing experiment, we explored methods to integrate the use of thermo-forming and machining (CNC / Robotics) sheets of plastic developed earlier (previous 2 semesters) to construct a larger topological structure. The approach was to understand the fundamental modules and how their varying differences can be achieved with a singular approach to construct and crop the module using a Dremel Tool attachment for the robot. With the use of computational tools, students proposed a massing for which the smooth and thickened layers were aggregated to produce the pavilion. A series of massing proposals were evaluated based on their structural, spatial, and visual quality. Images show Fundamental Modules (1), 3rd Leg Component with connected Upper-Region (2) and Dyno-Roid (3).
Students:
(1-3) Nubia Garcia, Tierney Sadowski, Emily Hertzberg, Maximillian Foreman, Jonathan Cortes
(4-6) Robinson Strong
(7) Seung-Hoon Lee, Robinson Strong
(8) Daniel Rodriguez
(9-11) Mari Kroin, Daniel Armitano , Sasha Chechel, Brandon Spinosa
(12-13) Hayden Minick
(14-15) Nubia Garcia, Robinson Strong
Ajmal Aqtash
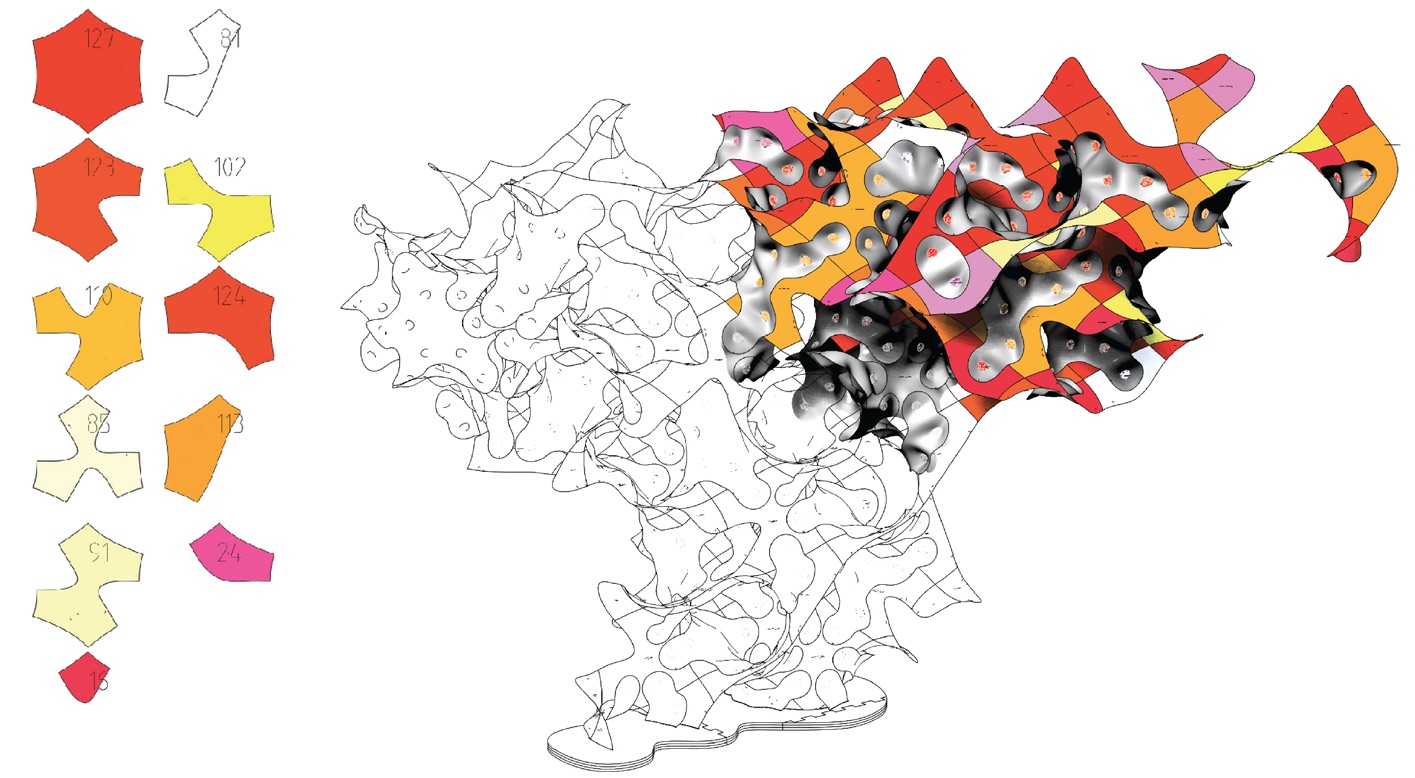
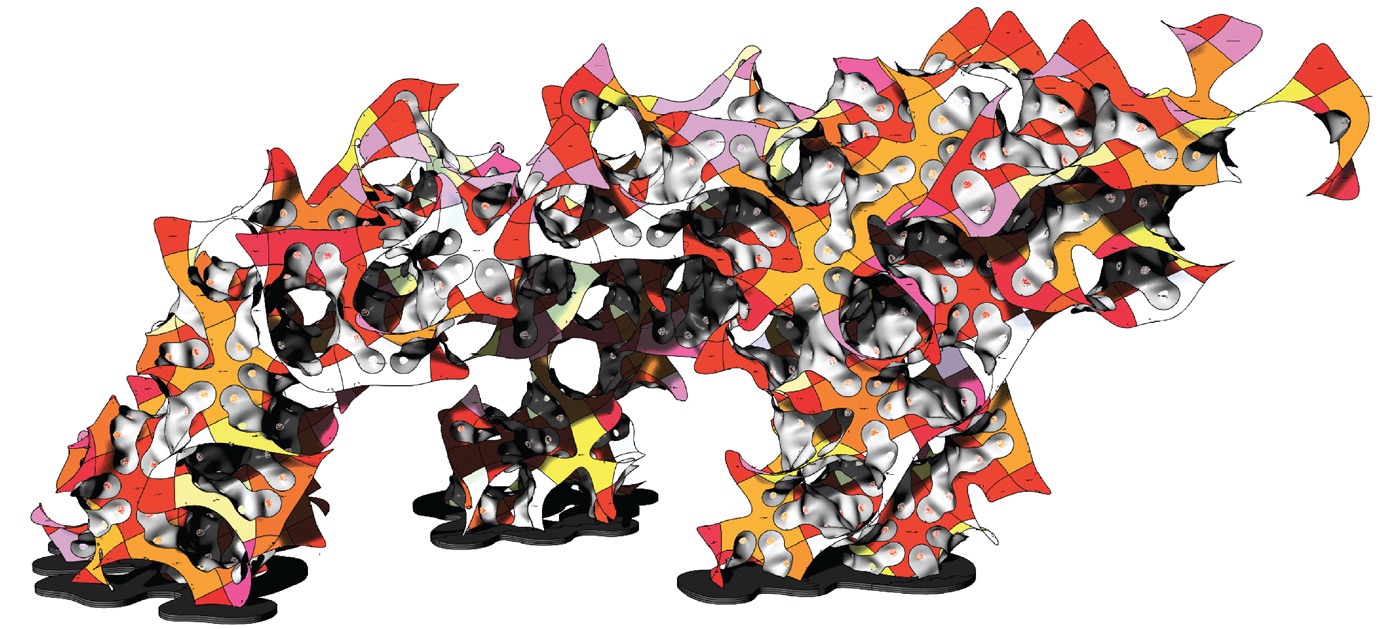
John Gulliford/Haresh Lalvani
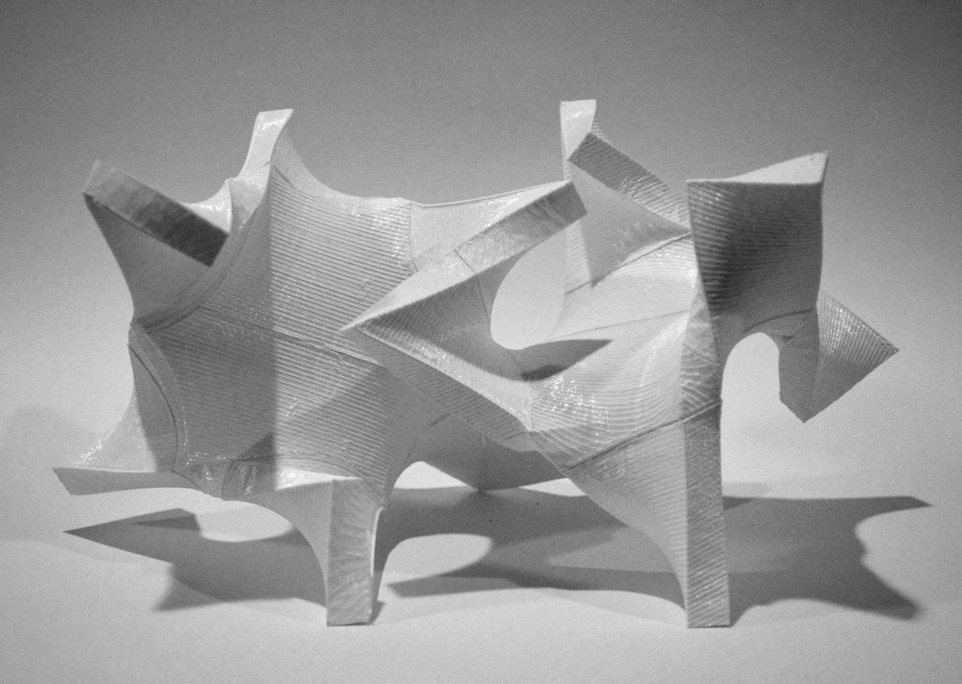
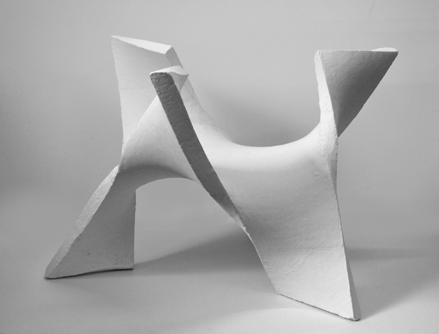
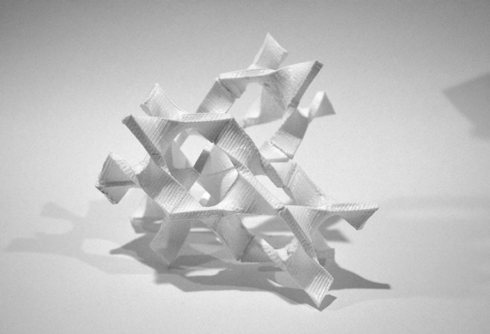
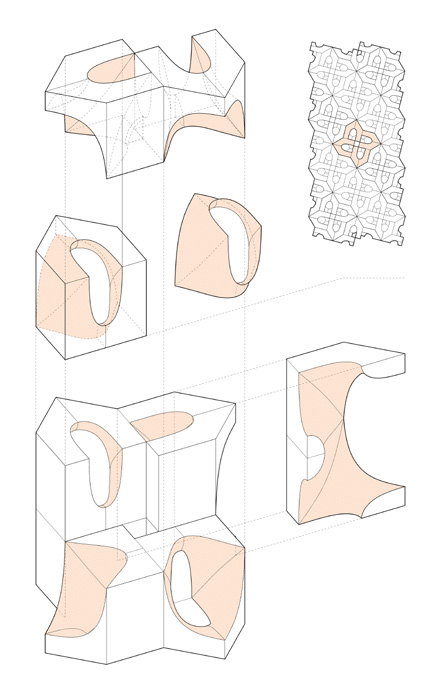
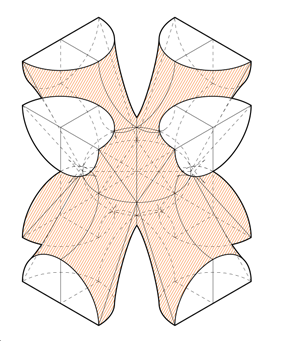
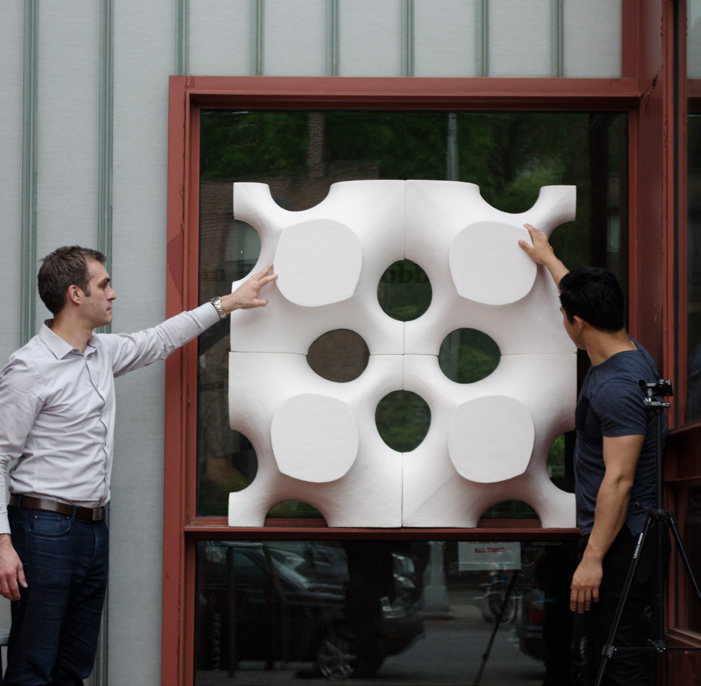
Che-Wei Wang / Haresh Lalvani
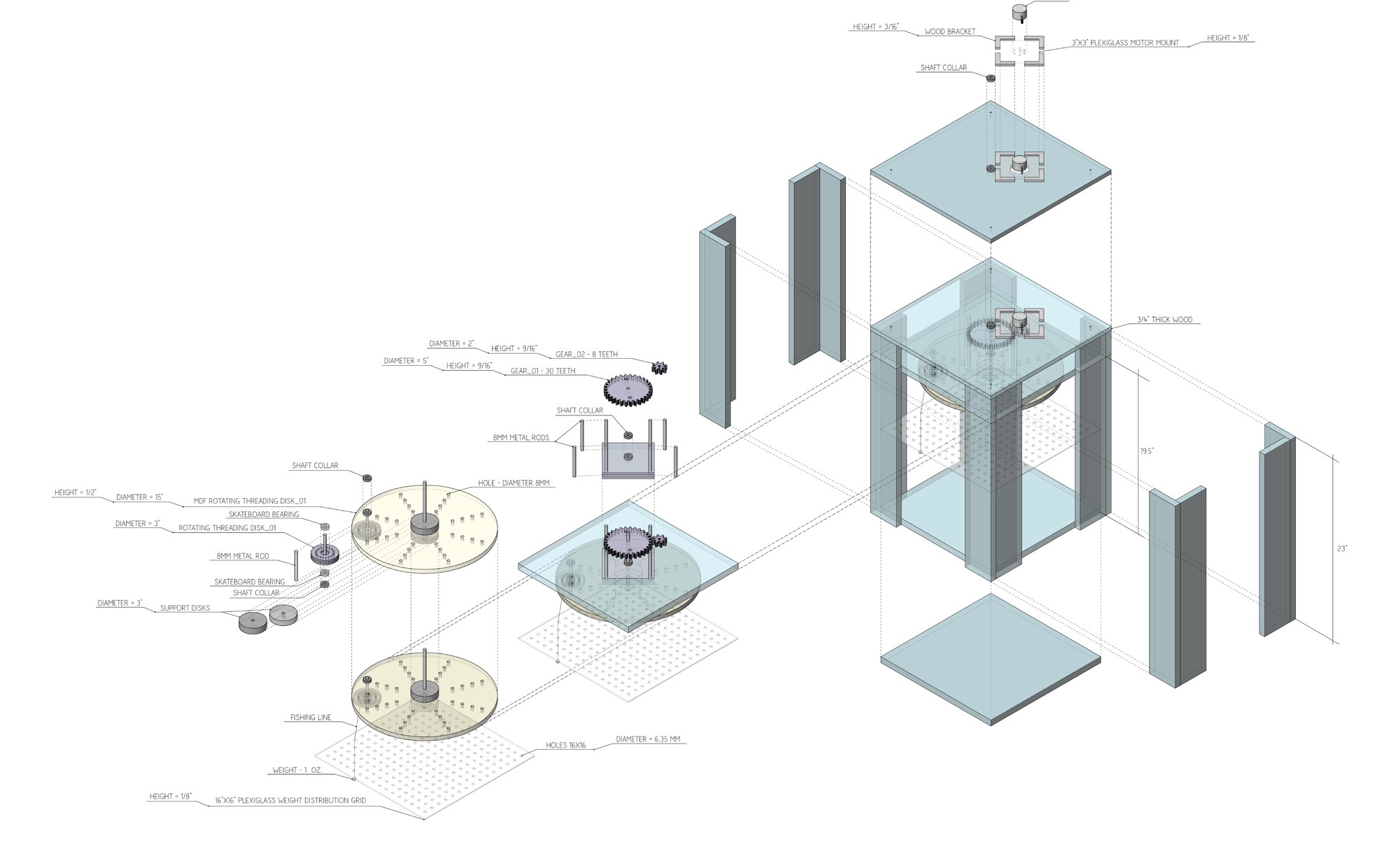
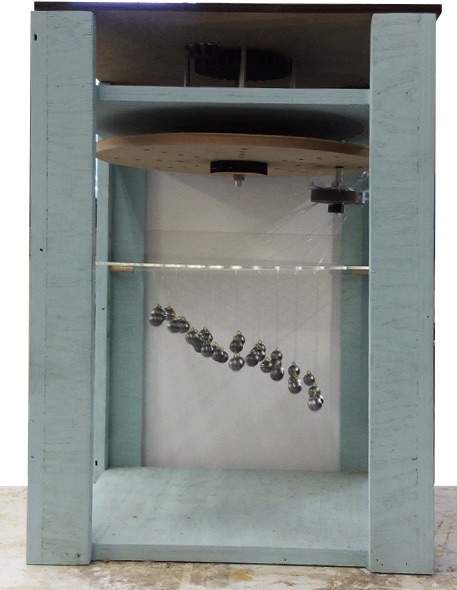
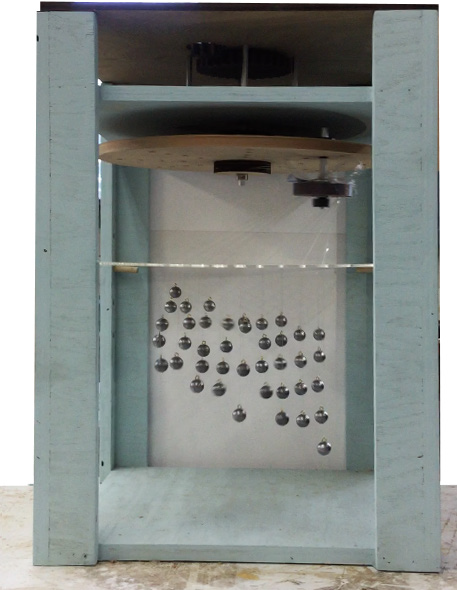
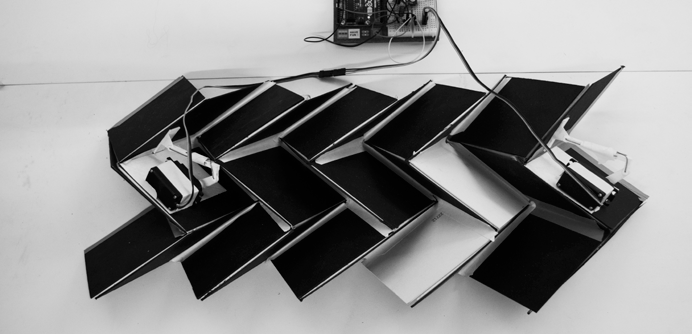
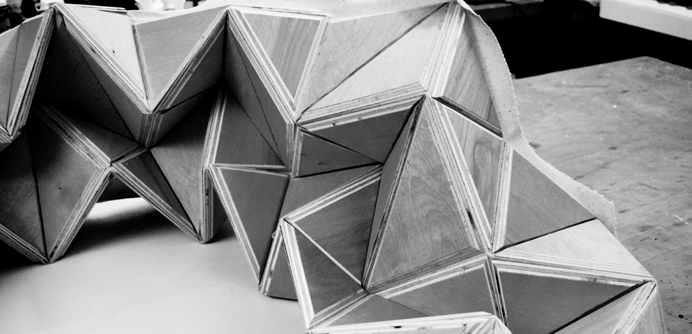
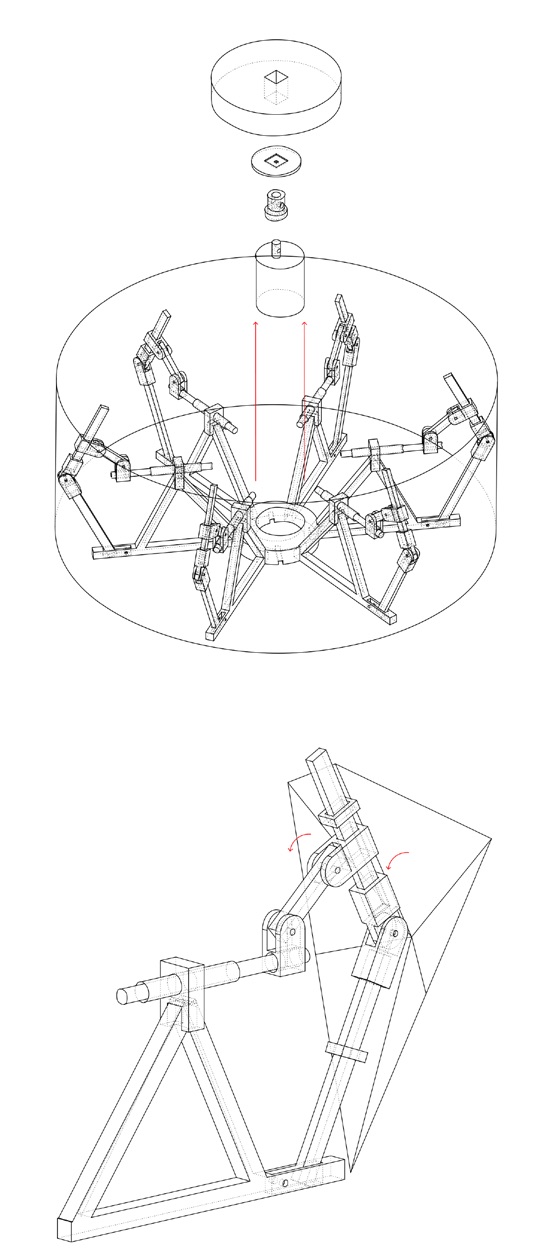