HARESH LALVANI 2016-17
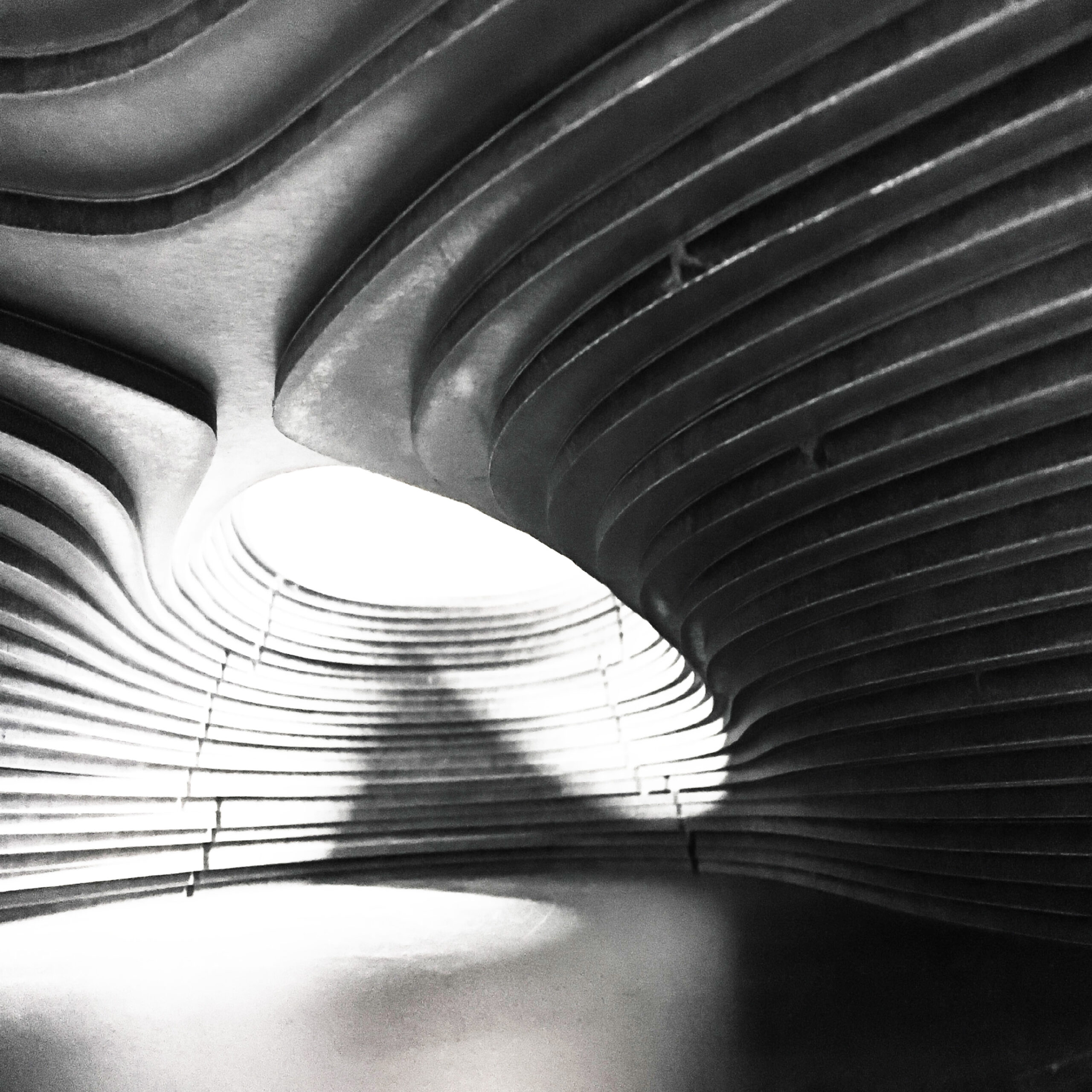
3D HYPERSURFACE (PHASE 3)
We present the first results of Phase 3 which involved full scale production of one level of the continuously curved one-sided surface we have been working on. Contoured for assembly, 6mm thick alucobond contours were water-jet cut at Milgo-Bufkin, our industry partner and material donor. One of the most challenging aspects was developing a strategy to mitigate the increasing cost of factory production. This required us to re-design and continuously re-test while stabilizing the assembly method and production sequence. The core concept of this phase was exhibiting the fact that digital fabrication of a complex curved structural surface from flat sheets was not only possible, but was being invented at an industry scale.
Our idea that would allow us to accurately erect three dimensional complex surfaces from several thousand unique pieces stemmed from embedding the 3d “positional information” (term borrowed from developmental biology) within each piece. This required the development of a strategy for the placement of each physical alucobond piece in 3D space without external supports like formwork or visual guides. We developed a system of aluminum pegs (hollow tubes, each ¼ inch in diameter and 12mm high), that would not only provide a vertical structural layer to layer connection, but would also guarantee an accurate curvature of the complex structural surface. The pieces are adhered using Loctite 60HP epoxy adhesive which is stronger than alucobond. This guarantees a continuous structural surface that can withstand the temperature ranges (20 degrees below zero to 120 degrees) for year-round outdoor installation in New York.
The increased water-jet cutting cost due to peg holes required us to modify our design and ensure that only a single continuous water-jet path was required to cut each piece. Students developed a solution that took the form of slots on the perimeter of each piece. The slots required an external guide (initially, a small template 10-layers high) and eventually a formwork to guarantee global curvature of each piece. In constructing subsequent levels, we hope to return to an economical version of the peg-system and enable assembly without a mold.
[Credits]:
Principal: Haresh Lalvani
Digital Support: Robinson Strong, David Franck
Students: Elizabeth Austin, Santiago Brown, Ariana Cohn,
Kalliopi Oikonomou, Dina Elfaham, Haven Gordon, Matthew
Malcom, Sharvari Mhatre, Kalam Lin Siu, Hazel Sun, Ahmad
Tabbakh, Jingwei Wu
Industry Partners: Milgo-Bufkin, LERA+